Welcome to the world of bending and forming mastery in modern manufacturing! In today’s fast-paced industry, where precision is paramount and innovation knows no bounds, mastering these age-old techniques has become more crucial than ever.
From creating complex shapes with unparalleled accuracy to pushing the boundaries of material manipulation, this blog post will take you on an exciting journey through the art and science behind bending and forming. So gear up and brace yourself for a captivating exploration as we unravel the secrets that shape our modern world!
Understanding the Basics of Bending & Forming
Bending and forming are essential processes in modern manufacturing that shape various materials into desired forms.
These techniques are widely used in automotive, aerospace, construction, etc. In this section, we will delve deeper into the basics of bending and forming, discussing their definitions, differences, similarities, and common techniques.
Defining Bending and Forming
Bending is a manufacturing process involving deforming a material by applying force to create a curved or angled shape. This can be achieved through various methods, such as press braking, roll bending, and rotary draw bending.
On the other hand, forming refers to any process that changes the shape or size of a material without removing any material. This can include techniques like stamping, punching, stretching, or deep drawing.
Differences between Bending and Forming
The main difference between bending and forming lies in the result – while bending produces shapes with curves or angles, forming creates flat or contoured surfaces.
Additionally, bending typically involves plastic deformation of the material while maintaining its thickness. In contrast, forming often requires material thinning to achieve the desired shape.
Similarities between Bending and Forming
Despite their differences in results, both bending and forming involve the application of external forces on a malleable material to change its shape without breaking it entirely. Both processes also require precise control over pressure and temperature to avoid damaging the material during shaping.
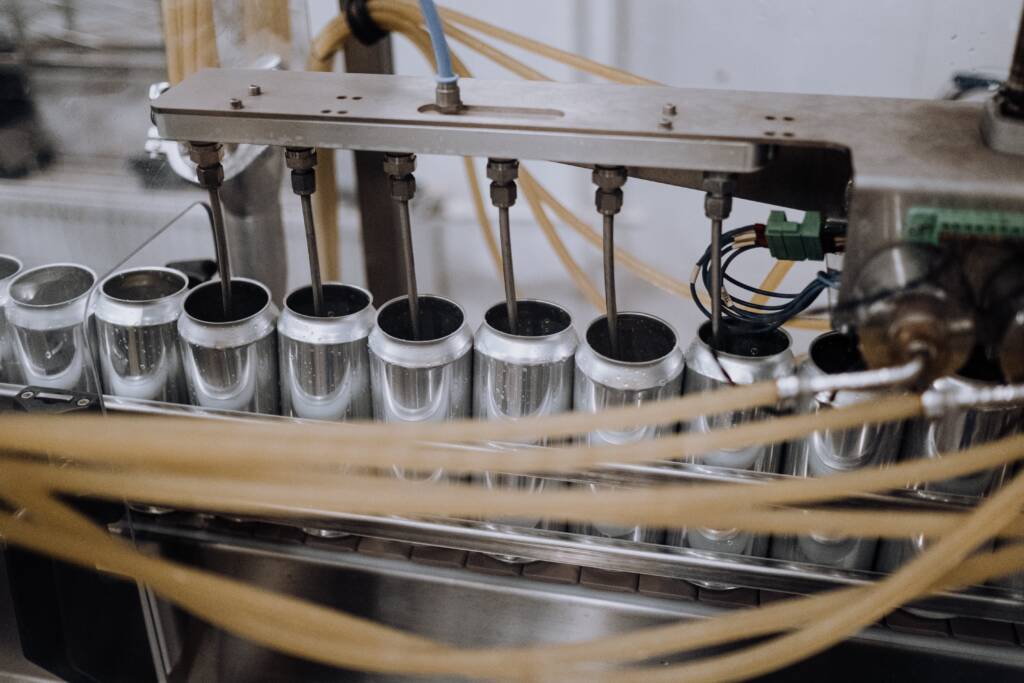
Factors Affecting Bending & Forming: Delving into key factors that impact the success of bending and forming processes, such as material properties, tooling, and machine capabilities.
Bending and forming are essential processes in modern manufacturing. They involve specialized equipment to shape and manipulate materials into desired forms, such as pipes, sheets, or tubes. These processes are crucial in various industries, including construction, automotive, aerospace, and more.
However, achieving successful bending and forming results is not as simple as it may seem. Several factors can significantly impact the outcome of these processes. In this section, we will delve into the key factors that affect bending and forming and discuss how they can influence the success of these operations.
- Material Properties:
One of the most critical factors affecting bending and forming is the material properties used. Every material has its unique characteristics that determine its behavior during these processes. For instance, due to their high malleability, ductile materials like aluminum are easy to bend without breaking or cracking. On the other hand, brittle materials like cast iron are prone to cracking when subjected to similar forces.
Other material properties that can impact bending and forming include elasticity, tensile strength, thickness or gauge of the material, grain orientation (in the case of metal sheets), etc. It is essential to have a thorough understanding of these properties before selecting a specific material for a project.
- Tooling:
The type and quality of tooling used for bending and forming also play a crucial role in ensuring successful results. Tooling refers to all the equipment used during these processes – from dies and punches to press brakes or rollers.
Different Types of Bending & Forming Techniques
Bending and forming techniques are essential in modern manufacturing, used to shape and manipulate various materials into desired shapes and forms. These techniques involve the application of force to a material, causing it to deform or change its shape without breaking.
They play a crucial role in creating almost every product we use daily, from household appliances to automobiles.
Various bending and forming techniques are used in modern manufacturing, each with its unique characteristics and applications. Let’s explore some of the most commonly used methods:
- Roll Bending: This technique involves passing a material between two or more rollers that apply continuous pressure to bend it into a curved shape. It is commonly used for creating cylindrical or conical shapes from sheet metal, pipes, tubes, and other long pieces of material.
- Press Brake Bending: As the name suggests, this technique uses a press brake machine to apply force on a sheet metal placed over a die to create precise bends at specific angles. It is suitable for creating straight arcs in different sheet metal thicknesses and is widely used in the automotive, aerospace, and construction industries.
- Rotary Draw Bending: This method utilizes specialized machinery called rotary draw benders to create tight radius bends in tubing or pipes by pulling them around a die using mandrels. It allows for high precision and consistency in producing small-diameter bends needed for plumbing systems or structural supports.