Are you ready to witness the epitome of precision and productivity in action? Brace yourself as we dive headfirst into the world of machining centers! In this electrifying blog post, we will unveil a new era of efficiency that redefines what it means to manufacture with sheer perfection.
From intricate components to mass production, these cutting-edge machines are revolutionizing industries across the globe. So buckle up and prepare for an adrenaline-pumping ride through the mesmerizing world of machining centers – where innovation meets excellence!
Types of Machining Centers
Machining centers are versatile machines used in the manufacturing industry to perform various machining operations. They combine the functions of a lathe, milling machine, drill press, and other cutting tools into one machine.
This makes them an essential tool for any production facility looking to increase efficiency and productivity.
Several machining centers are available, each designed for specific purposes and applications. In this section, we will discuss the various types of machining centers commonly used in modern manufacturing processes.
- Vertical Machining Centers (VMC)
Vertical machining centers are among the most popular machining centers used today. As the name suggests, these machines have a vertically oriented spindle that holds and rotates the cutting tool. The workpiece is mounted on a table that moves along the X, Y, and Z axes to allow for precise cutting movements. - Horizontal Machining Centers (HMC)
In contrast to VMCs, horizontal machining centers have a horizontally oriented spindle with a rotary table that allows for four-axis or five-axis machining. This setup offers more flexibility in terms of part orientation and allows for more complex cuts.
Advantages of Using Machining Centers
There are numerous advantages to using machining centers in manufacturing and production processes. These advanced machines offer high precision, speed, and flexibility that traditional machining methods cannot match.
In this section, we will dive into the advantages of machining centers and how they can improve efficiency in your operations.
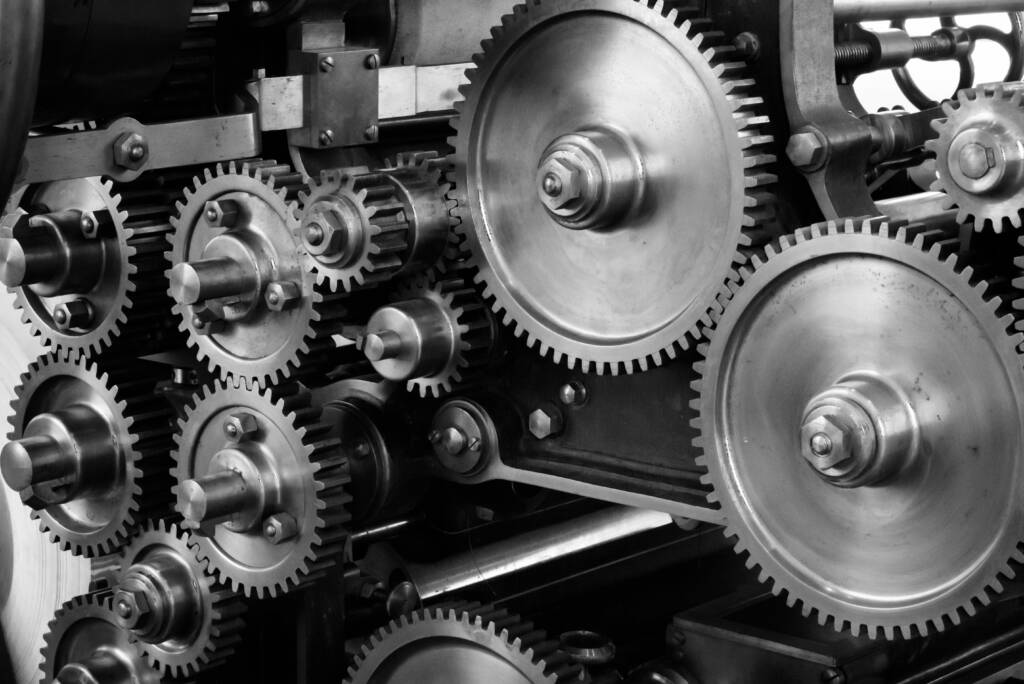
- Increased Efficiency:
One of the primary advantages of machining centers is their ability to increase the efficiency of production processes greatly. These machines utilize computer numerical control (CNC) technology, which allows for fast and precise cutting and shaping of materials. This eliminates the need for manual labor and reduces the risk of human error, resulting in faster production times and improved quality control.
- Versatility:
Machining centers are highly versatile machines that can perform multiple tasks with a single setup. They have various tools, such as drills, taps, end mills, chamfer mills, etc., all integrated into one machine. This eliminates the need for multiple specialized machines and setups, saving time and resources.
Factors to Consider When Choosing a Machining Center
When choosing a machining center, several factors must be carefully considered to ensure the best results and efficiency. A machining center is a highly versatile and powerful piece of equipment used in manufacturing processes such as milling, drilling, and cutting.
Understanding the different features and capabilities of various machining centers is important before deciding. Here are some key factors to consider when choosing a machining center:
- Type of Machining Center:
The first thing to consider is the machining center that best suits your needs. There are three main types – vertical, horizontal, and multi-axis – each with its own unique advantages. Vertical machining centers (VMCs) have a spindle mounted vertically above the workpiece, while horizontal machining centers (HMCs) have the spindle mounted horizontally. Multi-axis machines have multiple axes for increased flexibility and precision. - Workpiece Size and Weight:
The size and weight of your workpiece will determine which type of machining center is suitable for your operations. VMCs are generally better suited for smaller workpieces, while HMCs can handle larger ones due to their horizontal spindle orientation, allowing easier access and handling.
How to Optimize the Use of Machining Centers for Maximum Efficiency
When it comes to machining centers, efficiency is key. These powerful machines are designed to streamline manufacturing and quickly produce high-quality, precise parts.
However, optimizing its use for maximum efficiency is important to reap a machining center’s benefits truly.
Here are some tips on how you can get the most out of your machining center:
- Plan and Prepare Ahead: Have a clear plan before starting your machining center. This includes having detailed drawings or CAD models of the part you want to manufacture and understanding all the necessary specifications, such as dimensions and tolerances. By having a solid plan beforehand, you can minimize setup time and avoid any mistakes that may result in wasted materials or time.
- Utilize Automation: Modern machining centers have advanced automation features such as tool changers and pallet systems. Make use of these features to reduce downtime and increase productivity. You can quickly switch between tools with automatic tool changers without stopping production. Pallet systems allow for simultaneous loading and unloading of parts, reducing idle time.
Maintenance and Care Tips for Longevity and Continued Efficiency
Maintenance and care are essential for ensuring machining centers’ longevity and continued efficiency. Regular maintenance can prevent breakdowns, reduce downtime, and extend the lifespan of the equipment.
This section will discuss some tips for maintaining and caring for your machining center to ensure optimal performance.
- Cleanliness is Key:
One of the most crucial aspects of maintenance is keeping your machining center clean. Regularly removing chips, debris, and other contaminants from the machine’s interior and exterior surfaces is essential for proper functioning. Accumulating these particles can lead to clogged coolant lines, damaged components, and decreased accuracy in cutting operations. It is recommended to establish a daily cleaning routine that includes wiping down all surfaces with a mild detergent solution, blowing out chips from critical areas using compressed air, or vacuuming them. - Lubrication:
Proper lubrication reduces friction between moving parts in a machining center. Most modern machines come equipped with automatic lubrication systems; however, it is still necessary to check oil levels regularly and top up if needed. It is also crucial to follow the manufacturer’s recommendations regarding which type of lubricant to use and how often it should be changed.