Welcome to the future of precision! In a world where accuracy and efficiency reign supreme, grinding machines have become the unsung heroes of manufacturing. These cutting-edge marvels are shaping industries like never before, from intricate gears to perfectly polished surfaces. Join us as we dive into the world of grinding machines and explore how they are revolutionizing precision engineering.
Get ready to be amazed by their capabilities, intrigued by their technology, and inspired by their potential to shape our tomorrow. Let’s embark on this thrilling journey together as we uncover how grinding machines are truly shaping the future of precision!
What are Grinding Machines?
Grinding machines are powerful tools that have revolutionized the manufacturing industry. These machines are used for shaping and finishing objects through abrasion, which involves removing small amounts of material from a workpiece to achieve the desired shape and surface finish.
They are essential in automotive, aerospace, medical, and tool-making industries, where precision and high-quality finishes are crucial.
A grinding machine consists of a rotating abrasive wheel or disc powered by an electric motor. The workpiece is held securely in place by a chuck or other holding device while the abrasive wheel makes contact with it at high speeds.
As the wheel rotates, it grinds away the excess material on the surface of the workpiece until it achieves the desired size and shape.
Types of Grinding Machines: Centerless, Cylindrical, Surface, and more.
Grinding is an essential process in the manufacturing industry, used for shaping and finishing various materials to achieve precise dimensions and surface finishes.
With technological advancements, grinding machines have become more efficient and precise, playing a crucial role in shaping the future of precision engineering.
Various types of grinding machines are available today, each with unique features and capabilities. This section will discuss some of the most commonly used types of grinding machines – centerless, cylindrical, surface, and more.
- Centerless Grinding Machines:
Centerless grinding is a machining process that does not require any centers or fixtures to hold the workpiece in place. As a result, it offers high productivity and accuracy while reducing setup times. This type of machine consists of three main components – a grinding wheel, a regulating wheel, and work rest support. The workpiece is placed between these two wheels, where the rotation of the regulating wheel feeds the workpiece towards the grinding wheel at a predetermined speed for optimal results. - Cylindrical Grinding Machines:
Cylindrical grinders are one of the oldest grinding machines but have undergone several improvements over time. These machines feature a rotating abrasive wheel that removes material from the surface of a cylindrical workpiece to create a smooth finish or maintain tight tolerances on diameter sizes. They come in two variations – external cylindrical grinders for outer diameter (OD) surfaces and internal cylindrical grinders for inner diameter (ID) surfaces.
How do Grinding Machines Work?
Grinding machines are a crucial component in the manufacturing industry, used for shaping and finishing various materials. These machines use an abrasive wheel to remove material from a workpiece, creating a smooth and precise surface. But how exactly do grinding machines work?
The basic principle behind grinding machines is abrasion – wearing down or polishing a surface using friction. The abrasive wheel attached to the machine rotates at high speeds, making contact with the workpiece and removing tiny fragments of material.
Several types of grinding machines are available, each with its unique way of functioning. However, they all share some common elements that make them effective in achieving precision results.
- Motor and Drive System
The motor drives the abrasive wheel at high speeds while the drive system controls its movement and direction. Most modern grinding machines use electric motors that provide variable speed control for more accuracy. - Workholding Device
The work-holding device holds the workpiece securely in place during the grinding process. This could be a chuck, vise, or other specialized tool, depending on the shape and size of the workpiece.
Advantages of Using Grinding Machines: Increased accuracy, faster production, and cost-effectiveness.
Grinding machines have been vital in the manufacturing industry for many years, providing precision and efficiency in shaping and finishing various materials.
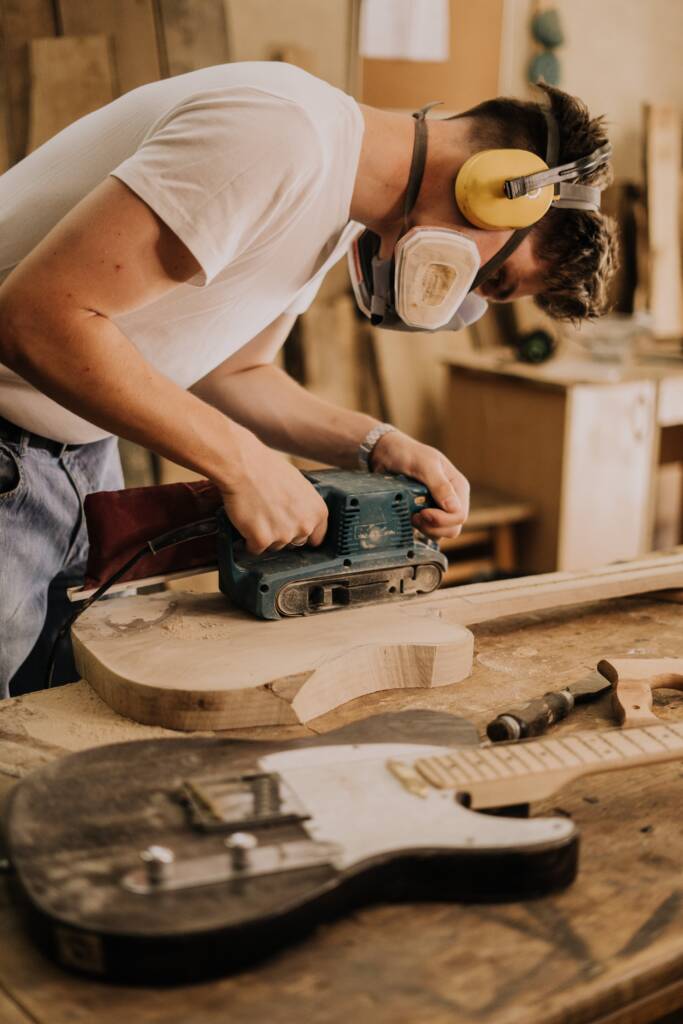
These machines use abrasive wheels to remove material from a workpiece, producing a smooth surface finish or precise shape. In recent years, there has been a significant advancement in grinding machine technology, making them even more efficient and accurate.
In this section, we will discuss the advantages of using grinding machines and how they shape the future of precision.
Increased Accuracy:
One of the most significant advantages of using grinding machines is their ability to achieve high levels of accuracy. Unlike other machining processes that rely on cutting tools, grinding uses an abrasive wheel to remove material from the workpiece. This allows for precise control over the dimensions and surface finish of the final product.
Grinding machines are equipped with advanced computer numerical control (CNC) systems that can provide micron-level accuracy, ensuring consistency and repeatability in production.
With such precision, manufacturers can produce parts with tight tolerances and intricate shapes that would be impossible to achieve through traditional machining methods.
Faster Production:
Another advantage of grinding machines is their ability to increase production speed significantly. To produce a finished product, traditional machining processes require multiple steps, such as drilling, milling, turning, and polishing.
On the other hand, grinding combines all these steps into one operation by removing material from the workpiece using an abrasive wheel. This results in faster production times and reduced setup times between operations.
Automotive, Aerospace, Medical, etc
Grinding machines have become an indispensable tool in various industries because they produce precise and smooth surfaces on different materials.
From automotive to aerospace, medical to construction, these versatile machines have proved to be essential for shaping and finishing various components used in modern-day manufacturing processes. Let’s take a closer look at grinding machine applications in some of the major industries.
- Automotive Industry:
The automotive industry has always been one of the largest grinding machine users. They are extensively used for producing precision parts such as crankshafts, camshafts, gears, bearings, and engine blocks. The high accuracy and surface finish achieved by these machines ensure the proper functioning of internal combustion engines and other critical vehicle components. - Aerospace Industry:
In the aerospace industry, where safety and reliability are paramount, grinding machines produce intricate and complex parts with tight tolerances. These machines manufacture components like turbine blades, landing gear components, hydraulic cylinders, engine casings, etc. that require high precision and superior surface finish.
Automation and AI integration
Recent years have seen significant advancements in grinding machine technology, particularly integrating automation and artificial intelligence (AI). These developments have revolutionized the precision grinding industry, allowing faster and more accurate production processes.
In this section, we will delve into some recent technological advancements in grinding machines, shaping the future of precision manufacturing.
Automation has been a game-changer in many industries, and it is no different in the world of grinding machines. With computer numerical control (CNC) technology, automation has made it possible to produce complex parts with high accuracy and efficiency.
CNC technology uses computer-aided design (CAD) software to create 3D models of parts, which are then translated into instructions for the machine to follow.