Are you ready to dive into the manufacturing world and explore the incredible power of hydraulics? Today, we invite you on a thrilling journey as we unveil how hydraulic systems have revolutionized the industry.
From boosting efficiency to delivering unmatched strength, hydraulic power is driving manufacturing forward at an unprecedented pace. So buckle up and prepare to be amazed by the limitless possibilities that lie ahead with our exploration into “Pressing Forward with Hydraulic Power in Manufacturing.”
The History of Hydraulic Power and its Evolution in Manufacturing
Hydraulic power in manufacturing can be traced back to ancient civilizations, with evidence of water-powered machinery being used by the Greeks and Romans. However, it wasn’t until the 17th century that significant advancements were made in hydraulics and its application in manufacturing.
One of the earliest known pioneers in hydraulic power was Blaise Pascal, a French mathematician and physicist who discovered the principles behind how liquids transmit pressure equally in all directions.
Benefits of Using Hydraulic Power in Manufacturing Processes
Hydraulic power has been an integral part of manufacturing processes for many years, and for good reason. It offers numerous benefits, making it a popular choice among manufacturers.
This section explores the advantages of using hydraulic power in manufacturing processes.
- High Power and Force
One of the main benefits of hydraulic power is its ability to generate high levels of force and power. This makes it ideal for heavy-duty applications such as pressing punchtraction cutting in the automotive, construction, and aerospace industries.
With hydraulic power, manufacturers can precisely control the force applied to a particular task, resulting in accurate and consistent results.
- Versatility
Hydraulic systems are incredibly versatile and can be tailored range of manufacturing processes. Tan can be used for lifting motion (such as lifting or pushing) and rotary motion (such as turning or bending).
Moreover, handle various materials – from soft plastics to tough metals – making them suitable for diverse industrial applications.
Components of a Hydraulic System and How They Work
A hydraulic system is a type of power transmission system that uses pressurized fluid, usually oil or water, to transfer energy and perform work. It is commonly used in manufacturing industries for various applications such as lifting heavy objects, powering machinery, and controlling motion.
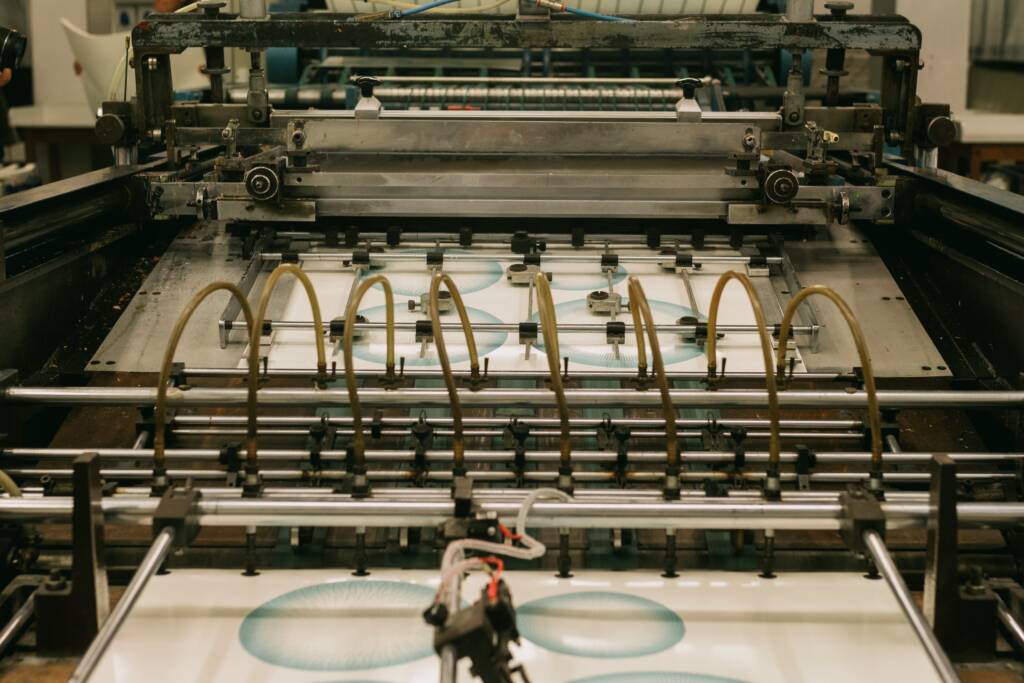
The basic components of a hydraulic system include a hydraulic pump, reservoir, valves, and actuators (cylinders or mses. Let’s look at each element and how it works to create the powerful force behind hydraulic systems.
- Hydraulic Pump
The hydraulic pump is responsible for converting mechanical energy into fluid power. It draws oil from the reservoir and pressurizes it to blow it out toward the system. Two main types of pumps are used in hydraulic systems: gear pumps and piston pumps. Gear pumps use rotating gears to move fluid, while piston pumps use reciprocating pistons to create pressure. - Reservoir
The reservoir serves as a storcool for the filter fluid. It also helps cool and filter the liquid to keep it clean and free from contaminants that could damage other components in the system. The resedeep’s size depends on the system’s size and intended use.
Common Applications of Hydraulic Power in Manufacturing
Hydraulic power has been an essential tool in the manufacturing industry for decades, providing immense strength and control in various applications.
This versatile technology utilizes pressurized fluid to generate mechanical force, making it a popular choice for many industrial processes. This section will explore some of the most common hydraulic power applications in manufacturing.
- Forming and shaping: One of the primary uses of hydraulic power in manufacturing is forming and shaping materials. The high force generated by hydraulics enables precise bending, punching, shearing, and other metalworking operations. Hydraulic presses are commonly used to form sheet metal into various shapes for products such as automotive panels, appliances, and machinery parts.
- Clamping and holding: Another important application of hydraulic power is clamping and holding components or workpieces in place during machining or assembly processes. Hydraulic clamps provide a strong gripping force that can store even heavy objects securely without damaging them. This makes them ideal for CNC machines, welding fixtures, and assembly lines.
Challenges and Limitations of Hydraulic Systems
Hydraulic systems have been a crucial part of the manufacturing industry for decades, providing powerful and efficient means of generating pressure and force.
However, like any other technology, hydraulic systems have challenges and limitations that can impact their performance and reliability.
In this section, we will discuss some of the common challenges and limitations faced by hydraulic systems in manufacturing facilities:
- Temperature Sensitivity:
One of the major limitations of hydraulic systems is their sensitivity to temperature changes. Hydraulic fluids are known to expand or contract with varying temperatures, which can affect the overall performance and accuracy of the system. Maintaining a consistent fluid temperature becomes crucial for smooth operation in extreme weather conditions, such as extremely hot or cold environments. - Leakage:
As hydraulic systems rely on pressurized fluids to transmit power, any leakage in the system can significantly impact its efficiency and reliability. Even small leaks can lead to a loss of pressure, resulting in reduced output or even failures. Therefore, regular maintenance checks should be conducted to identify and fix potential leakages.
Innovations and Advancements in Hydraulic Technology for the Future
Innovations and advancements in hydraulic technology have always been at the forefront of the manufacturing industry. From powering heavy machinery to controlling complex systems, hydraulics has proven to be a reliable and efficient source of power.
As we continue to push towards a more technologically advanced future, there are exciting new developments on the horizon that will change the way we think about hydraulic power.
One area where significant advancements are being made is in the field of electro-hydraulic systems. These systems combine traditional hydraulic components with electronic controls, allowing greater precision and control over hydraulic movements.
They also offer increased energy efficiency, making them an attractive option for manufacturers looking to reduce their carbon footprint and operating costs.