Are you ready to dive into the fascinating world of CNC lathes and discover how this cutting-edge technology is revolutionizing precision manufacturing? Look no further because we are unveiling the secrets behind CNC lathes’ incredible accuracy and versatility in today’s blog post.
Whether you’re a tech enthusiast or simply curious about the future of machining, get ready to be mesmerized by the intricate workings of these powerful machines.
Join us as we explore the unlimited possibilities and unmatched precision CNC lathes bring to industries worldwide. Let’s embark on this journey and witness firsthand how these remarkable tools shape our modern world!
What is a CNC Lathe?
A CNC lathe, or Computer Numerical Control lathe, is a type of machine tool used for shaping and cutting materials such as metal, wood, or plastic. It works by rotating the workpiece on its axis while using various cutting tools to remove material and create the desired shape.
This process is automated through computer programming, making it more precise and efficient than traditional manual lathes.
The technology behind CNC lathes has greatly advanced over the years, allowing for increased precision and accuracy in manufacturing processes.
Instead of manually operating the machine and adjusting settings for each cut, all instructions are entered into a computer program that controls every aspect of the machining process. This allows for consistent and repeatable results with minimal human error.
How Does a CNC Lathe Work?
A CNC (Computer Numerical Control) lathe is a revolutionary technology that has transformed the manufacturing industry.
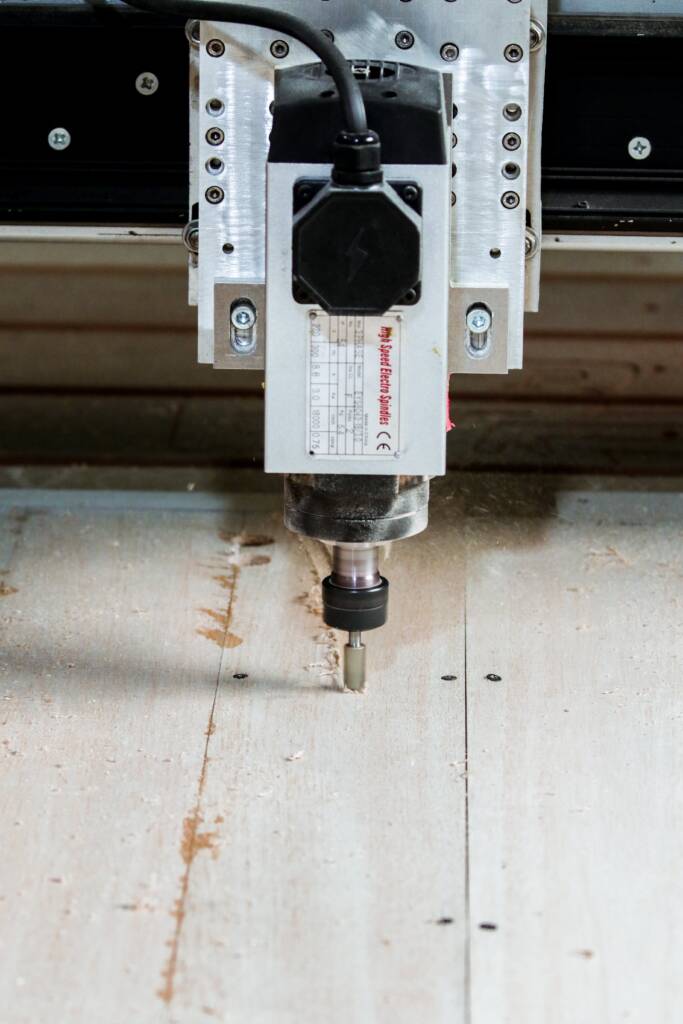
It allows for precise and efficient machining of various materials, making it an essential tool in many automotive, aerospace, and medical industries.
So, how does a CNC lathe work? Let’s dive into the details.
- Designing the Part:
The first step in using a CNC lathe is designing the part you want to create using CAD/CAM software. This software allows you to create a 3D model of your desired product with all its specifications and dimensions. - Programming:
Once the design is complete, it must be translated into machine instructions that the CNC lathe can understand. This process is known as programming and involves converting the 3D model into G-codes – a language consisting of letters, numbers, and symbols that tell the machine what actions to perform. - Setting Up:
Before starting production, the necessary tools must be loaded onto the machine’s tool turret or magazine according to their specific positions on the machined part. The material used for machining also needs to be securely mounted onto the spindle.
Advantages of Using CNC Lathes
CNC lathes are a type of computer numerical control (CNC) machine that uses programming instructions to perform precision machining tasks on various materials such as metal, wood, and plastic.
They have become an essential tool in the manufacturing industry due to their ability to produce high-quality products with exceptional accuracy and repeatability. This section will discuss the advantages of using CNC lathes in detail.
- Increased Precision and Accuracy
One of the main advantages of using CNC lathes is their unparalleled precision and accuracy. The machines are programmed with specific instructions that dictate every movement, allowing for precise cutting and shaping of materials. This eliminates human error when using manual lathes, resulting in consistently accurate parts every time. - High Production Speeds
CNC lathes can perform multiple operations simultaneously, significantly increasing production speeds compared to manual lathes. This makes them ideal for large-scale production runs where time is crucial. Additionally, CNC lathes can run continuously without needing breaks or rest periods, increasing productivity.
Precision and Accuracy in CNC Lathes
Precision and accuracy are two crucial factors determining the quality of a finished product in the manufacturing industry. These two concepts are essential in consistently achieving precise and accurate results in CNC lathes.
Precision is the ability to repeat a specific movement or machining process with minimal variation. In other words, it is the consistency of dimensions within tight tolerances. On the other hand, accuracy refers to how closely a measurement or machining process conforms to its intended target value.
CNC lathes utilize advanced technology and cutting-edge techniques to achieve high precision and accuracy in every aspect of their operation. Let’s take a closer look at some key components contributing to precision and accuracy in CNC lathes.
- Control System:
Its control system is at the heart of every CNC lathe, which is critical in achieving precision and accuracy. The control system consists of software programs that receive instructions from the operator and translate them into machine movements. These programs can be customized to meet specific requirements, allowing for highly precise and accurate machining processes. - Servo Motors:
Servo motors drive a CNC lathe’s various axes (X, Y, Z) with exceptional precision and accuracy. They work together with encoders, which provide feedback on position and speed to ensure that each movement is executed accurately according to specifications.
Types of CNC Lathes and Their Capabilities
Several types of CNC lathes are available in the market today, each with unique capabilities and features.
Understanding these different types is essential in choosing the right CNC lathe for your machining needs. This section will explore the most common types of CNC lathes and their capabilities.
- 2-Axis Lathes:
Also known as standard or straight bed lathes, 2-axis lathes are the most basic type of CNC lathe. They have two axes – X and Z – that control the movement of the tool in a horizontal and vertical direction, respectively. These machines are best suited for simple turning operations such as facing, boring, drilling, threading, and chamfering. - Multi-axis Lathes:
As the name suggests, multi-axis lathes have more than two axes (typically up to 9), allowing for greater flexibility in machining operations. The additional axes enable these machines to perform multiple cutting processes simultaneously, resulting in higher precision and efficiency.
Applications of CNC Lathes in Different Industries
CNC lathes, or computer numerical control lathes, have become integral to modern manufacturing processes. These advanced machines use computer programming to control the movement and operation of cutting tools, resulting in highly precise and efficient production.
CNC lathes’ applications span various industries, from aerospace and automotive to medical and electronics. Let’s take a closer look at how CNC lathes are utilized in different sectors.
- Aerospace Industry:
The aerospace industry is known for its stringent quality standards and demanding precision requirements. CNC lathes play a crucial role in this sector by producing complex components such as turbine blades, engine parts, landing gear components, etc. These machines can easily handle materials like aluminum, titanium, and stainless steel, delivering high-quality products with tight tolerances. - Automotive Industry:
In the automotive industry, where mass production is essential to meet customer demands, CNC lathes are used extensively for their fast production speeds and accuracy. They are used for making critical components like axles, pistons, gears, and shafts with consistent quality throughout the production process. Moreover, these machines can easily switch between turning, drilling, or milling operations without manual intervention.
Future of CNC Lathes Technology
The future of CNC lathe technology is constantly evolving and advancing, with new developments and innovations being introduced to enhance precision, efficiency, and productivity.
As the demand for high-quality machined parts continues to increase in various industries such as aerospace, automotive, and medical, the need for advanced CNC lathe technology becomes even more crucial.
One of the key advancements that we can expect in the future of CNC lathes is increased automation. With the integration of artificial intelligence and machine learning capabilities, CNC lathes can operate autonomously without constant supervision or manual programming. This will reduce human error and greatly improve production speed and accuracy.