Welcome to the fiery world of welding, where sparks fly and metals unite in an awe-inspiring display of strength and precision! In this blog post, we dive deep into the captivating realm of industrial bonds, exploring the incredible power wielded by skilled welders.
From towering skyscrapers to colossal bridges, these unsung heroes create a lasting impact on our modern world through their magical artistry with metal.
Different types of welding techniques and their applications
Welding is a vital process in the industrial world, used to permanently join two or more pieces of metal together. However, not all welding techniques are created equal.
Each type has its own unique characteristics and applications that make it suitable for different situations. This section will discuss the most commonly used welding techniques and their specific uses in various industries.
- Shielded Metal Arc Welding (SMAW)
Shielded Metal Arc Welding, also known as stick welding, is considered the oldest and most basic form of welding. It involves using an electric arc to melt a metal electrode rod and create a bond between two pieces of metal. The electrode rod serves as both the filler material and the heat source, making it suitable for outdoor or remote locations where other power sources may not be available. - Gas Metal Arc Welding (GMAW)
Gas Metal Arc Welding, also known as MIG (Metal Inert Gas) welding, uses an electric arc formed between a continuously fed wire electrode and the base metal to create a weld joint. The wire acts as the filler material and the electricity conductor while shielding gas protects the molten weld pool from atmospheric contamination.
Advantages of welding in industrial settings
Welding is a technique used to combine two or more pieces of metal by melting and fusing them. This process has been around for centuries, but with technological advancements, it has become an essential part of industrial settings.
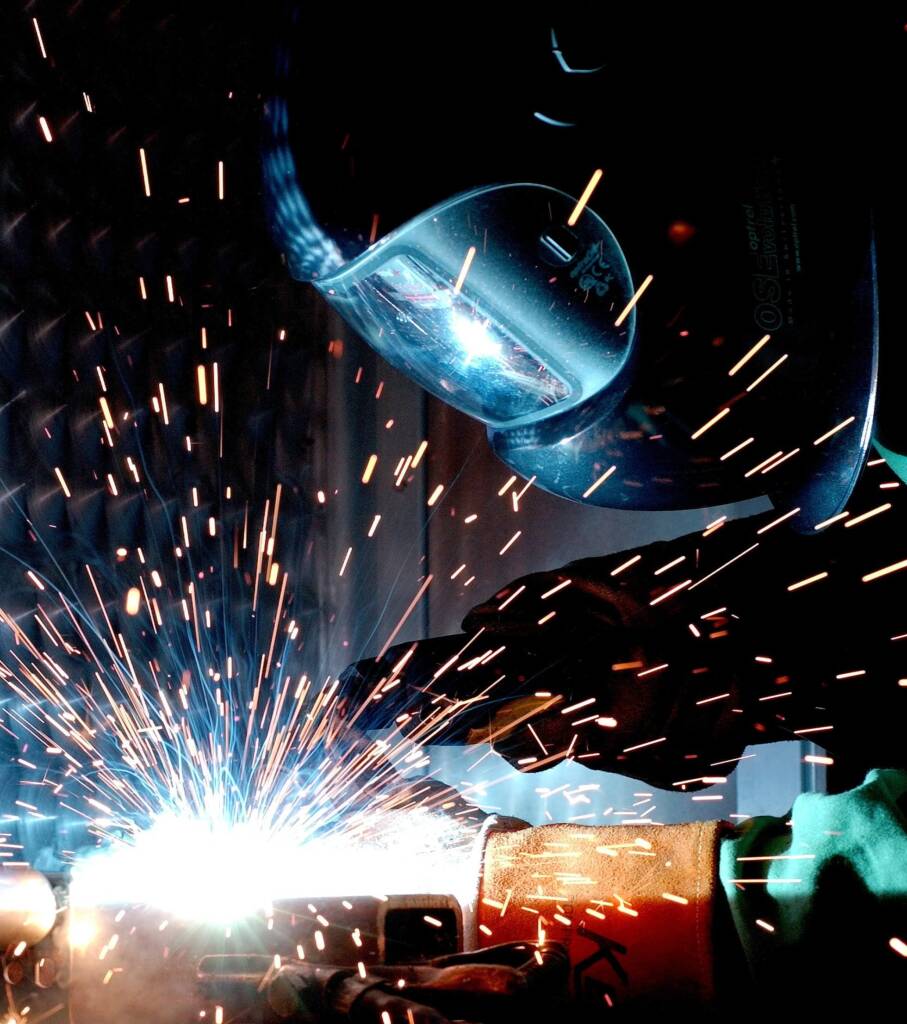
In this section, we will look at the various advantages of welding in industrial settings and how it contributes to the strength and durability of industrial bonds.
- Stronger Bonds: One of the primary benefits of welding in industrial settings is its ability to create strong bonds between two pieces of metal. Welded joints are often stronger than the base materials, making them ideal for heavy-duty industries such as construction, manufacturing, and shipbuilding.
- Versatility: Welding offers a high degree of versatility when joining different types of metals. It can be used on various materials, such as steel, aluminum, copper, and stainless steel. This makes it an invaluable tool for industries that require multiple metals in their operations.
Challenges faced by welders and how they overcome them
Welding is a highly skilled profession that requires precision, technique, and physical strength. Welders are responsible for joining two or more pieces of metal together to create strong and durable structures.
However, this job comes with its own challenges that welders must face daily. In this section, we will discuss some common challenges welders face and how they overcome them.
- Exposure to hazardous materials:
One of the biggest challenges faced by welders is exposure to hazardous materials. Welding involves working with high temperatures, intense light, fumes, and gases that can harm health if proper precautions are not taken. These hazards can lead to respiratory problems, skin irritations, eye injuries, and even long-term health issues such as lung cancer.
How they overcome it:
To protect themselves from these hazards, welders wear personal protective equipment (PPE) such as helmets with special lenses, gloves, aprons, and respirators. They also work in well-ventilated areas to minimize exposure to fumes and gases.
- Physical Demands:
Welding is a physically demanding job that requires standing for long hours in uncomfortable positions while holding heavy tools and equipment. This can strain the body, resulting in back pain, muscle strains, or injuries.
The role of technology in modern welding processes
The advancement of technology has greatly impacted the welding industry, transforming it from a labor-intensive process to a more efficient and precise one.
With the integration of modern technology, welding processes have become faster, safer, and more reliable. In this section, we will explore the various ways technology has revolutionized the world of welding.
- Automation:
One of the most significant changes technology brings is automation in welding processes. This involves using computer-controlled systems to perform welds instead of manual labor. Automated welding machines have sensors and cameras that can detect defects or deviations from desired parameters, making them highly accurate and consistent. They also eliminate human error, resulting in higher-quality welds.
- Precision Welding:
Precision equipment such as laser beams and robotic arms has enabled incredibly precise welds in tight spaces that were once impossible for humans to access. These advanced tools allow for greater control over heat input and directionality during welding, resulting in stronger bonds with minimal distortion.
Famous structures built using welding techniques
In construction and engineering, welding has been a crucial technique to create some of the most iconic and awe-inspiring structures.
Welding plays a major role in ensuring their stability and strength, from towering skyscrapers to massive bridges. Let’s explore some of the famous designs built using welding techniques.
- The Golden Gate Bridge
One of the most recognizable landmarks in San Francisco, the Golden Gate Bridge is an engineering marvel that spans 8,981 feet and connects the city to its northern neighbors. This suspension bridge was built using over 80,000 miles of wire cable that skilled workers welded together. It took four years to complete and stands as a testament to the strength of welded steel. - Burj Khalifa
The tallest building in the world, standing at 2,717 feet tall, Burj Khalifa in Dubai, is another example of how welding techniques can be used to create monumental structures. Over 40,000 tons of steel were welded together to form this towering skyscraper, which required immense precision and expertise to ensure its stability.
Impact of welding on the economy and job market
The impact of welding on the economy and job market is significant and far-reaching. Welding is crucial in various industries, such as construction, manufacturing, transportation, and energy production. It is a fundamental process combining materials to create strong, durable structures and products.
One of the major contributions of welding to the economy is its role in infrastructure development. Welded structures are essential for buildings, bridges, roads, and other critical infrastructure projects. Without welding, it would be challenging to construct these essential facilities that support economic growth and development.
In the manufacturing sector, welding is used to produce numerous goods ranging from small household appliances to large industrial machinery.
Combining different materials allows for the creation of complex and intricate designs that make modern technology possible. This has increased productivity and efficiency in manufacturing processes, leading to economic growth.
Safety measures and regulations for welders
Safety is paramount in any industrial setting, and this is especially true for welders. Welding involves working with high temperatures, dangerous fumes, and heavy equipment, making it essential to have strict safety measures and regulations in place to protect the well-being of the workers and prevent accidents.
Here are some of the key safety measures and regulations that every welder should be aware of:
- Personal Protective Equipment (PPE):
The first line of defense for a welder is proper personal protective equipment. This includes a welding helmet with a filter lens that protects the eyes from harmful UV rays, gloves made from heat-resistant materials, an apron or jacket made from flame-resistant material, steel-toed boots to protect feet from falling objects, and earplugs or earmuffs to protect against loud noises. Wearing PPE protects the welder and ensures compliance with safety regulations. - Proper Ventilation:
Welding produces toxic fumes that can cause serious health issues if inhaled. Having adequate ventilation in the welding area is crucial to remove these fumes and maintain clean air quality. If ventilation is not possible due to space constraints, then respiratory protection must always be worn.